Arc spray, sometimes referred to as twin wire arc spray, is a process that uses an electric arc to melt wires. The molten metal is then atomized with compressed air to create a spray stream that applies the coating onto the surface being sprayed.
Anti-corrosion or engineering coatings can be applied by arc spray and changing between the two is quite simple. Arc spray systems are commonly considered to be easy to operate and also to automate.
National Alloy Solutions has a full range of arc spray systems for hand-held and fully automatic / robotic applications.
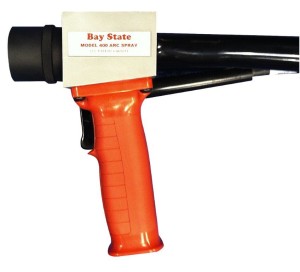
The Use Of Arc Spray Coating Techniques
Wire arc spray coating is the oldest wire arc technique. It requires the material to be fed into a machine as two separate wires. A highly positive charge is applied to one of the wires, and a highly negative charge is applied to the other wire. The two wires are continuously fed into each other at the tip of the device during the deposition process. The significant voltage differential between the two wires creates an electric discharge between the wires. This spark dramatically heats and melts the material at the tip of the wire.
At the same time, compressed gas is continuously fed outward into the tip, and then towards the surface that the material that is to be deposited on. The melted metal will be essentially picked up by the compressed air and thrown directly onto the surface.
As a result, anyone viewing the arc spraying device will notice a large spark trail directed onto the coated surface. As the deposited material cools, it will bond to the surface. Due to the need to create a potential difference across the wires, this technique is primarily used for metal coatings.
There are several advantages to the wire arc spray process when compared to other thermal spray techniques, such as high-velocity oxygen fuel spraying (HVOF). The first is that wire does not require the use of chemical fuels to heat the deposited materials. The only consumable that one uses in addition to the wire to be deposited, is compressed gas. All that is necessary to create the heat is the voltage differential powered by a standard electrical outlet. In fact, the wire arc spray process actually uses significantly less electrical power than HVOF. Only five to ten kilowatts of power is necessary for wire arc spraying, while up to fifty kilowatts is used by HVOF.
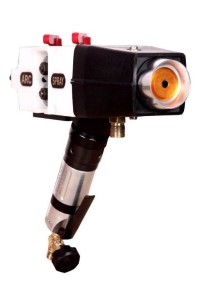
Wire arc spraying also delivers the highest deposition rates of any method of thermal spraying. Material can be deposited on surfaces at rates exceeding 15 kilograms per hour. The low heat created by the electrical arc system also is necessary for certain coating applications. For example, when a coating is applied to printed circuit boards, electronic components such as capacitors, have a low tolerance for applied heat.
Wire arc spaying is also very easy to accomplish. There are minimal training requirements in order for an operator to begin working. Because of the lower temperatures and the lack of flammable materials in the process, this technique also poses fewer safety risks compared to other thermal spraying processes. All of these features – the lower power consumption, the lack of need to purchase fuel, and the high deposition rate – make wire arc spraying the most cost effective way deposition process.
There are also some other things that the technique can accomplish. One can use two different materials for the two wires. This setup can effectively combine a mixing step with the deposition process. For example, it is not unusual for steel and bronze wires to be combined in such a manner when coating on bearing surfaces.
Use of this technique results in higher bond strengths than one can achieve with flame spraying techniques. These strengths are usually strong over a wide range of spraying angles. The porosity of the coating achieved is also lower than what you get from a flame coating technique.
A relatively new and quite different technique of arc spraying is the plasma transferred wire arc (PTWA). This is used primarily to coat internal surfaces of cylinders. One of its biggest uses is in the coating of car engine blocks.
Only one wire is used for the PTWA technique. A heated plasma jet is used instead of electric charge difference between two wires to heat the metal. The plasma jet also propels the metal to the surface of the target material for the deposition. The plasma jet is created by a potential difference created by an internal cathode. Due to the high kinetic energy of the plasma jet, materials deposited by this process rapidly flatten against surfaces despite sharp angles of impact. This process can be used to coat cylinders as large as 14 inches and as small as two inches.
The process of arc spraying has played an important role in manufacturing for a long time. This technique, in particular, is a highly cost-effective way of applying a metal coating.
National Alloy Solutions has the most cutting edge equipment to ensure that clients obtain exceptional results from their arc coating accessories and surfaces. We understand the dynamic environment that your items are often subjected to. We have carefully sorted and selected techniques that withstand harsh environments such as coats arc spray, which allows your items to undergo repair, modification, or coating without changing their initial design or workings. Arc Spray is used in HVOF environments comfortably because National Alloy Solutions has invested in research to use variants that suits each customer’s specific requirement.
If you are looking for a unique arc spray coating that enables your surface to survive extremities in temperature and intense heat conditions, give us a call. National Alloy Solution offers clients a complete range of thermal spray, HVOF, and plasma spraying technology options that is executed with state of the art equipment. We invest in research because we know that clients deserve the best.
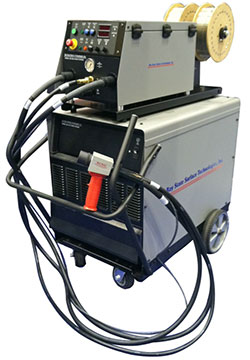
Model 400 Twin Wire Arc System
The Model 400 is a high performance wire arc spray system that brings flexibility, lower maintenance costs and reduced operator fatigue to your process. Driven by a reliable 400 amp, 3-phase Power Supply with SCR rectifiers, the system provides operating parameters from 18 – 40 Volts and 15 – 400 Amps at 100% duty cycle. All system functions are controlled from the Wire Feeder that is capable of being remotely controlled from up to 50 ft. away.
A key feature of the Wire Feeder lies in the quick-change four-drive roll per wire feed mechanism. Bypass air is metered into the drive housings and through to the coaxial cables. The air is used to blow dust or other foreign matter off the consumable feedstock prior to entering the cables. Faceplate controls include E-Stop, Power Reset, Wire Jog, Maintain Air and Purge Air. Power Supply controls consist of Voltage and Amperage with digital LED displays of each. Switches are environmentally sealed and all electronics are housed in NEMA 12 enclosure.
The Model 400 Arc Spray gun head is characterized by a patent-pending state-of-the-art quick change wire guide system that allows consumable wire guides to be replaced in less than 30 seconds using no tools. An on/off trigger switch is supplied on the detachable gun handle to control the wire feed, compressed air and power supply contactor. The gun head also provides several hard points for mounting to manipulators, robots and/or fixtures.
MODEL 400 ARC SYSTEM REFERENCE SHEET IN PDF FORMAT: