NAS offer two variants of HVOF Pistol Control Consoles to operate either liquid fuel or gas fuel pistols.
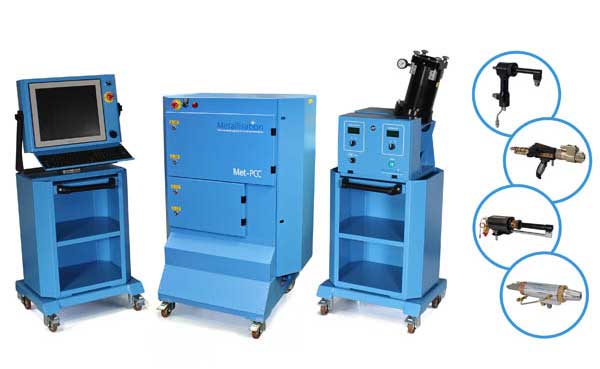
Overview:
The Metallisation Met-PCC(HVOF) system is the latest development to our range of HVOF systems.
The Met-PCC(HVOF) system applies all of the simple control / operator interface features of our previous HVOF and Plasma systems. The ‘–L’ version can be interfaced with our own MET-JET4L pistol and/or other non-Metallisation liquid fuel pistols. The ‘-G’ version can be interfaced to a range of non-Metallisation gas fuelled HVOF pistols.
The Met-PCC(HVOF) system has re-packaged the control elements and utilised the latest technology to optimise functionality and reliability. At the front end, the operator interface utilises an intuitive Graphical User Interface (GUI), including the option to integrate video images into the display. The interface runs on a familiar touchscreen Windows PC platform with Intel Dual Atom processor which is great for usability, integration and communication. Behind the scenes, the latest PLC runs the system with communication between devices via the reliable Ethernet protocol.
As you would expect from a system of this standard, the gases/fluids are all mass-flow controlled for optimum repeatability of coatings. All spray parameters can have real-time trending on the system.
The result is a truly unique, compact design, flexible, easy to operate HVOF system, backed up by Metallisation’s 90 year+ industry experience and support.
Key Applications:
- Hard-chrome plate alternative
- CGL mill rolls
- Oil/Gas valves
- Paper rolls
- Suspension components
- Landing gear
- Hydroelectric turbines
- Automotive valves
- Wire drawing blocks
Key Features
- Mass flow control = repeatability
- Easy to use operator interface
- Liquid fuel = thick, low stressed coatings
- Various pistols can be used
- High hardness, low oxide level coatings
- PC control with touch screen
- Optional keyboard control
- Unlimited recipes and parameter recording
- Low running costs compared to hydrogen fuel
- High bond strength and low porosity coatings
Specifications
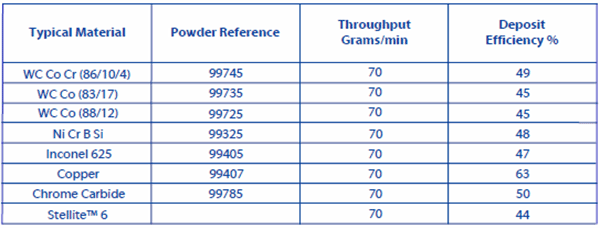
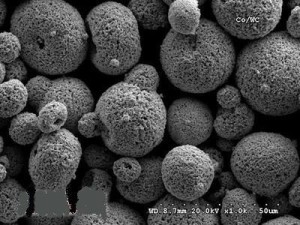
In simple terms, this refers to a thermal spray coating process that is used to restore or improve components’ surface dimensions or properties. This in turn extends the equipment’s life by increasing their resistance to wear and erosion, while providing corrosion protection.
The process involves applying a high-velocity gas stream and high temperature, to spray molten or semi-molten materials onto these equipment’s surfaces. The aim is to produce a high-density spray coating creating a ground for a high surface finish.
The coating forms a hard structure with outstanding adhesion and exceptional hardness, that provides substantial corrosion protection and wear resistance of your metallic materials, alloys, and ceramics. All you need is to utilize the HVOF coating technique.
We understand the processes and the needs relating to HVOF coating, and we have everything you might need ready for purchase. We are always a call away, and you will have all your needs met. Our services aim to satisfying our customers and always paint a broad smile on their faces. We do this through creating a customer-buyer friendly environment by giving you the most reasonable prices for quality products.
What are the BENEFITS of HVOF coating?
- Reduced costs – Simply explained by the fact that you will lessen the number of repairs, or the need to replace your equipment as often.
- Improved performance – With reduced wear and tear, your equipment’s performance will be enhanced.
- Improved electrical properties.
- Enables components to operate, in both high and low temperatures.
- Your components can operate within harsher chemical environments – The reason behind this is due to the HVOF coating creating exceptional hardness combined with outstanding resistance to beat corrosion.
- Improves efficiency.
- Finally, HVOF coating improves the mating components’ life. No wear, no corrosion.
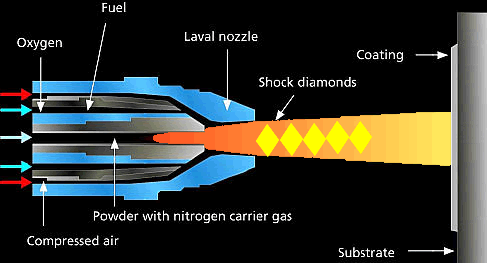
HVOF Coating Process Details
A mixuture of liquid or gas fuel and oxygen is inserted into a combustion tank or HVOF Coating chamber, where it is ignited and combusts over and over. The outcome is that hot gases create a pressure of around 1 Mpa and push through a converge-diverge nozzle and then travels though a straight away segment. The fuels created can be in liquid or gaseous state (propane, methane, hydrogen, natural gas, acetylane etc.) The minimum project velocity at the end of the barrel (>1000 m/s) passes the speed of sound in most cases. A powder stock is inserted in the gas stream, which speeds up the powder into ranges of 800 m/s. The powder and gas stream is then directed toward the surface of the substrate to be coated. Parts of the powder partially melt in the stream, and deposits onto the substrate. The outcome is that the coating has high bond strength and low porosity.
Some HVOF Coating Systems
1. MultiCoat HVOF coating system Platform
The MultiCoat HVOF runs the HVOF liquid and gas fueled spray guns.
Key characteristics and features:
- Supports both liquid and gas-fueled HVOF processes.
- Its monitoring, safety and controlling upgrades with enhancements.
- Accommodates a variety of material feeders as well as HVOF spray guns.
- From just a single controller, the MultiCoat will run up to 5 thermal spray processes.
- Supports controlled atmosphere plasma spraying.
- Mass-flow controlled.
2. UniCoatPro LF (Liquid Fuel) HVOF Spray System
This is a fully-featured and compact spray platform delivered as a complete system where the control unit, powder feeder, and spray gun are included.
Key characteristics:
- Remote maintenance capability.
- Multilevel alarm system.
- Storage for up to 100 recipes.
- Touchscreen graphical user interface featuring visualization software.
- Closed-loop process control featuring real-time monitoring.
- Sophisticated reporting and trending package.
- Process Media: Kerosene, oxygen.
3. Diamond Jet Series thermal spray system
This system uses gas-fueled HVOF producing hard, dense, and thick, industrial machine parts coatings.
Key characteristics:
- Rotameter gas metering system.
- Process parameters real-time monitoring.
- Automatic operation of DJ, Diamond Jet Gun.
- Multisystem operation: slave/master configuration capability,
- Control type: PLC-based, semi-automatic control.
- Process gasses: Propane, Hydrogen, Propylene, Nitrogen, Oxygen, Compressed Air.
We have all these systems, among many others, ready for purchase
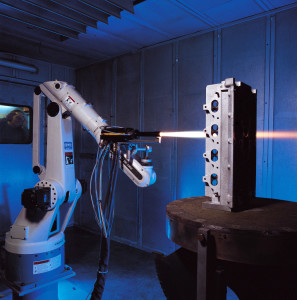
Industries That Use HVOF Coating
You can find HVOF coatings in several different industries that include thermal Robobot HVOF Sprayingspray processes. Any industry in need of wear or corrosion resistance, or homogeneous structures, will need HVOF coatings. These industries include agricultural industries, construction equipment, aerospace, food processing, among many others. For highly sophisticated electronic devices, HVOF coating technology is also utilized. In the medical field, HVOF coatings are applied to the medical instruments requiring higher performance dielectric properties.
Whatever industry you are in, we can meet all your HVOF coatings needs, efficiently and effectively. We combine our experience and professionalism to give you the right product for your needs, at an affordable price. We prioritize quality, and you can be sure that your equipment will serve you longer and efficiently with our HVOF coatings. Reduce costs and improve performance by placing that order. As I mentioned above, the solution to your needs is just a call away, and we will be happy to serve you. We offer 1 Day delivery inside our designated delivery area as well. Contact us to today for a FREE quote today!