National Alloy Solutions is your one-stop shop for all of your plasma spray equipment needs.
Plasma spraying is a type of thermal coating process that produces tenacious coating of high quality by use of a combination of heat energy produced at very high temperatures an inert medium such as argon along with high velocities of particle.
Thermal spray coating techniques are applied in industrial processes to come up with thick coats that range from approximately 20 micrometers to many mms. The techniques are marked with a significantly high deposition rates compared to traditional processes such as chemical vapour depositing and electroplating.
The Procedure
The materials used for the plasma spraying process and other thermal spray coating processes include:
Alloys
Metals
Ceramics
Plastics
Composites
These materials are subjected to heat once they are fed in. They are heated to semi-molten or molten states. They are then pumped at fast speed towards substrates in micrometer-sized particles. Interestingly, while coating the surface, the substrate, may not necessarily heat up much. This property enables the plasma spraying process to be used on even flammable materials.
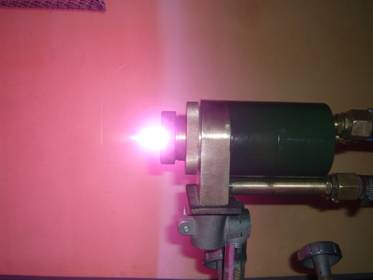
Plasma Spray Process Details
In this type of thermal spraying, the feedstock which is normally either in liquid or plasma powders form, or even wire, which is directed into the jet called the plasma jet. This jet originates from the plasma torch. The jet temperatures are normally in the range of 10,000 Plasma spray techniquesK. Like in other forms of thermal spray coating, the material in the jet is forced to a substrate. The droplets in molten form, flatten and become solid, which then become a deposit. Usually, these deposits stick with the substrate and they form the coating. Sometimes there are free parts which can be extracted by separating the substrate.
The parameters that regulate, and influence, the particle interaction in the plasma jet, are varied and subsequently with the substrate. This, therefore, implies that the deposit properties will also vary depending on such factors. Ideally, the most obvious parameters include the type of feedstock used, the composition of the plasma gas, the level of energy input, the distance of the torch offset, the rate of flow and the cooling of the substrate among other factors.
The term plasma describes the gas that is raised to a very high temperature, that is then able to ionize, and consequently becomes an electrical conductor. The plasma spray process adds advantage to spray coating activity because it enables spray painters to spray virtually any ceramic or metallic solution onto a wide range of textures and materials with remarkable boding strength, even as it minimizes substrate distortion. There is a wide range of materials used for thermal spray coating, and hvof, on the market. The client should, therefore, exercise discretion to select materials that suit their needs.
What Are the Benefits of Plasma Spray Powders and Technology?
Plasma spray stands apart from many other spray options because it is just about the spray process techniques that offer the possibility of spraying diverse types of material. One can apply plasma spray from ceramics to metals on a large or significantly small offering. Here are some more benefits that this thermal technique brings to the coating arena.
High resistance to tearing and wear
High resistance to oxidation and heat
Protects surfaces against corrosion
Regulates temperature and acts as a form of insulation
Limits electrical conductivity and enhances resistivity
Where Can Plasma Spray Technology Be Applied?
Due to the fact that this technique of plasma spraying provides an opportunity to spray coat a large range of coating materials, most technologists do not spare a chance to apply it. Here are some uses that plasma spray is practically applied to in the hvof and thermal coating process.
- The wear resistance property of the process makes it the perfect choice for spraying ceramics of chrome oxide on print rolls used for laser engraving.
- It is also popularly used to spray gas turbines, cobalt ring grooves, tungsten carbide. This is also referred to as fretting wear
- Protects against high temperature as a barrier coating on gas turbinewhat is plasma coating combustion chambers and hardware
- protection against corrosion and resistance to abrasion and/ or erosion.
- Generally, plasma spray is a solution that spans from high-temperature conditions to relatively low and stable ones and delivers impressive results either way.
- The technique is invaluable in coating structural materials because the coating from spray coating protects against temperature extremes. Most exhaust heat management that controls thermal dynamics uses plasma spray coating.
- The technique is also used for processing plasma powders, i.e. modifying the chemistry of substances, homogenization and spheroidization among other applications.
- The technique using intricate variants may also be used to create structures with pores. These used in medical circles for bone ingrowths and making some form of implants in patients.
It is also important to note that plasma spraying is a variant of several forms of thermal spray techniques. It is particularly attractive to many users because of its resistance qualities to high-temperature environments and usage in HVOF applications. Indeed, ceramic coating is best done with plasma spray because they require extremely high temperatures to melt. In particular ceramic materials melt at temperatures above 3500 Fahrenheit. The technique is used to apply many varying types of ceramic coatings.
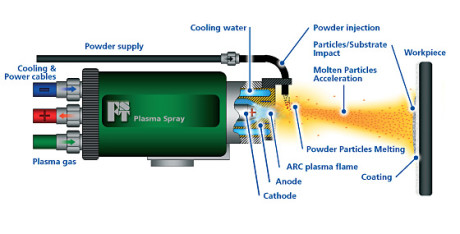
The different types of the Plasma Spraying Process
Thermal spraying systems can be categorized into several criteria. In summary these include:
plasma jet generation
Plasma forming medium
Vacuum plasma spraying
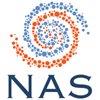
National Alloy Solutions employs the cutting edge plasma spray technology to ensure that clients obtain exceptional results from their plasma coated accessories and surfaces. We Plasma Spray Technologyknow the dynamism of the dynamic environment that your items are often subjected to. We have carefully sorted and selected techniques that withstand harsh environments such as coats plasma spray, which allows your items to undergo repair, modification, or coating without changing their initial design or workings. Plasma spray is used in HVOF environments comfortably because National Alloy Solutions has invested in research to use the plasma spray variant that suits each customer’s specific requirement.
If you are looking for a unique thermal spray coating that enables your surface to survive extremities in temperature and intense heat conditions, give us a call. National Alloy Solution offers clients a complete range of thermal spray, HVOF powders, plasma powders, and plasma spraying technology options.