National Alloy Solutions is your one-stop shop for all of your thermal spray equipment needs.
In addition to selling thermal spray systems and parts we also offer calibration services on most thermal spray equipment. Please contact us for more information.
Thermal spraying is technique which is used to coat various surfaces. The coating which is to be applied, known as the feedstock, is heated to a very high temperature and then sprayed onto the surface. The heating process can then be completed through electrical means (such as plasma or arc heating) or via combustion.
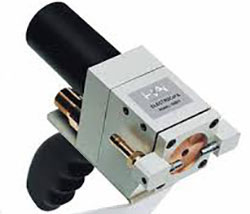
One of the main benefits of thermal spraying is that the coating that it leaves can be quite thick. The thinnest thermal coatings are around 20 micrometers thick, while they can be up to several mm thick if required. The thickness will depend on the feedstock being used, and how it is heated. Thermal spraying technologies allow for rapid deposition of compounds, and it can be used to apply coatings including metals, ceramics, plastics, composites and alloys. These feedstocks are fed into the sprayer either as a powder, or in the form of a wire, and are heated until they reach a molten or semi-molten state, after which they are forced through the sprayer to be applied to the object. The resulting coating is made through the accumulation of a number of the sprayed particles on the surface.
Versatile Spray Technology
It is interesting to know that while the spray is heated to an incredibly high temperature, the object that is being sprayed does not get hot, in fact, it is possible to spray objects that are flammable, without problems.
Measuring the Quality of the Coating
The quality of the coating is measured in terms of its oxide content, its porosity, the bond strength, the roughness of the surface, and its hardness. The higher the velocity of the particles, the better the quality of coating will typically be.
There are several different ways of delivering thermal spray. The most common are:
Plasma spray
Detonation spray
HVOF Spraying
Wire arc spraying
Flame spraying
The flame spraying and wire arc thermal spray technologies are very old, in fact, they were developed around a century ago. They are still used today, however, because they are simple and effective. The velocity of the particles in the spray is quite low, and the materials to be sprayed are heated until they are molten, so the quality of the coating is not quite as good as it is with HVOF spraying.
More modern thermal spray technologies, such as plasma spraying, were not developed until the 1970s. in these techniques, the spray reaches incredibly high temperatures, so you can spray a wider variety of materials.
High Velocity Oxy-Fuel Coating Spraying is a process created during the 80s. With this powder spraying | wire spray | metal spray process type of technology, a mixture of oxygen and fuel is fed into a special combustion chamber. The mix in that chamber is ignited, and will combust continuously, resulting in a high pressure hot gas which is then pushed through a converging-diverging nozzle. The fuels used for this process can be gases such as propylene, acetylene, propane, methane or natural gas, or they can be a liquid such as kerosene. The jet velocity of the coating can be in excess of the speed of sound. The feedstock is usually a powder, and the stream of hot gas and powder will produce a coating which has a very high bond strength and a low porosity.
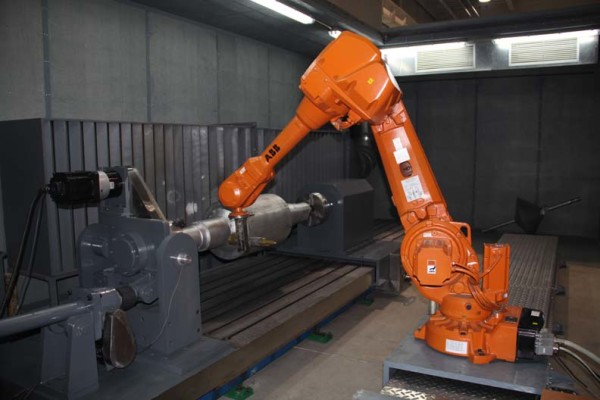
The thickness of a HVOF coating can be up to 12mm, and these coatings are quite corrosion resistant and also able to withstand a lot of wear and tear. The technology is often used for alumina and chromium carbide coatings. Warm spraying is similar to HVOF, but is done at a lower temperature, making it a more efficient process and one of the more popular thermal spray technologies.
Cold spraying coatings are a relatively new technology. They were developed in the 1990s by Russian technicians, who observed, accidentally, that coatings formed rapidly in cold conditions. The discovery was made while the scientists were experimenting with the problem of particle erosion when a target is exposed to high velocity flow, loaded with fine powder. The wind tunnel experiment gave them the idea for accelerating particles to high speeds, without them needing to be heated first. When the solid particles hit a surface at a high enough temperature, they deform and bond to the substrate, which is what creates the coating. The speed that the particles must reach for this to work depends on the size of the particle, and the temperature, as well as the type of particle. This type of spraying works best with relatively soft metals, but it has been made to work with a number of materials. The type of gas being used matters as well. Helium offers rapid particle acceleration, for example, but it is expensive to use and has a high flow rate. Other gases are cheaper, but may need heating in order for them to allow for sufficient acceleration.
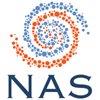
National Alloy Solutions employs the cutting edge thermal spray technologies to ensure that clients obtain exceptional results from their plasma coated accessories and surfaces. We Masking Products | thermal spray technologies | hvofknow the dynamism of the dynamic environment that your items are often subjected to. We have carefully sorted and selected techniques that withstand harsh environments such as coats plasma spray, which allows your items to undergo repair, modification, or coating without changing their initial design or workings. Thermal spray is used in HVOF environments comfortably because National Alloy Solutions has invested in research to use the thermal spray variant that suits each customer’s specific requirement.
If you are looking for a unique thermal spray coating that enables your surface to survive extremities in temperature and intense heat conditions, give us a call. National Alloy Solution offers clients a complete range of thermal spray, hvof, plasma powders, and thermal spraying technology options that is executed with state of the art equipment. We invest in research because we know that clients deserve the best.